Newsletter #5 – June 2020
Download pdf version here. Previous newsletters: Newsletter #1, Newsletter #2, Newsletter #3, Newsletter #4
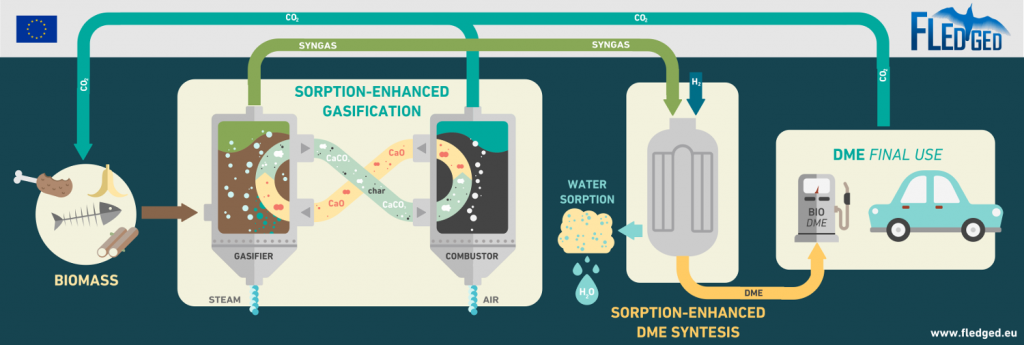
FLEDGED activities on biomass gasification are completed and many interesting results are available …
- Final experimental results on SEG process experiments in BFB at CSIC-ICB and in the University of Stuttgart pilot facility, for both stationary and flexible operation. Gasification performance assessed using wood pellet, grape seeds and Econward treated waste. Successful tests involved steam-to-carbon, temperature and solid inventory influence evalutation.
- The optimal catalyst-sorbent mixture has been selected for SEDMES testing and catalyst deactivation mitigation strategies developed. Preliminary tests in the TRL4 facility exhibit good conversion and regeneration performance.
- Large scale SEG simulation with calibrated 3D models to improve performance through optimized design.
The results obtained will be presented during a live workshop at the eEUBCE conference on 9th July, 2020 at 14:00.
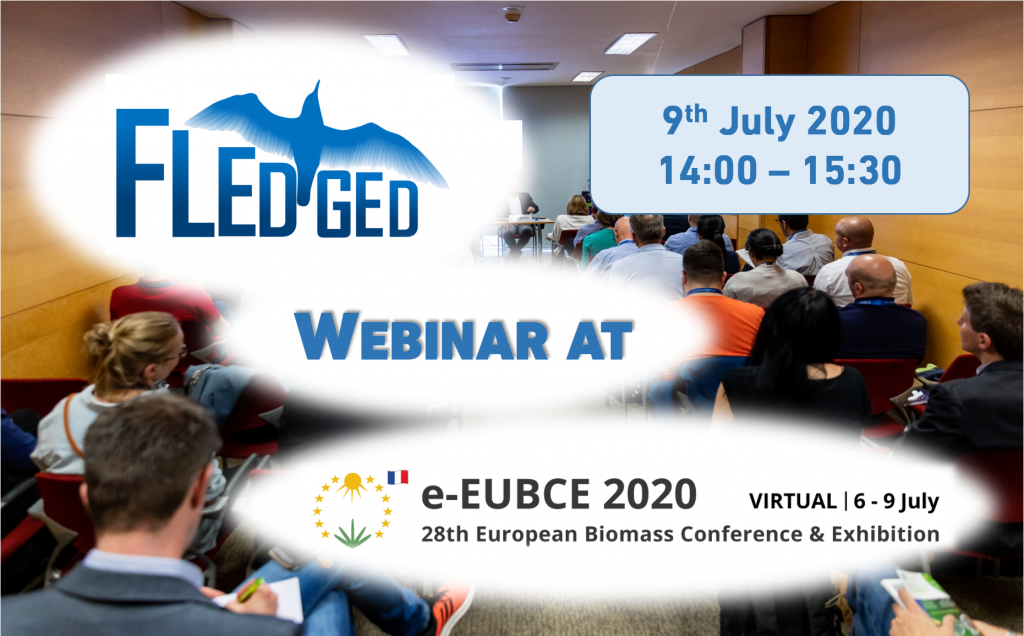
More details and additional short presentations from the partners on the dedicated webpage.
Final experimental results on SEG process experiments at pilot scale for stationary and flexible operating regimes
Tests of the sorption enhanced gasification (SEG) process in the 200 kWth dual fluidized bed pilot plant at USTUTT for stationary and flexible operating regimes are completed. Experiments were conducted using two different biomasses. Wood pellets that served as reference biomass and pellets produced out of the organic part of municipal solid waste by Econward (ECO pellets). The main differences between those two biomasses are the much higher ash content of the ECO pellets (21 – 33 wt%db) compared to wood pellets (0.2 wt%db). The ash content of the ECO pellets could be decreased with each batch by optimization of the production process of Econward. Also the content of nitrogen, sulfur and chlorine in the ECO pellets is much higher than in wood pellets.
Five experimental campaigns have been conducted in total for investigating the influence of several parameters (e.g. gasification temperature, steam-to-carbon ratio, weight hourly space velocity) on the syngas composition and the process stability. The duration of each campaign was up to 120 h, including heat-up of the reactors, which lasts about 22 – 24 h. During the campaigns, the facility has been operated 24/7 in a 3 shift mode with 5 persons per shift.
It could be demonstrated that the SEG process can be operated stably over a long period, which can be seen in the diagram above. In this diagram, the temperature trends in the gasifier and the combustor are presented for an exemplary SEG campaign. As can be seen, the combustor temperature has been more or less constant during the whole campaign after heating up the reactors. Only during one period, the temperature fluctuated due to problems with the screw conveyor. The gasifier temperature has been adjusted according to the experimental matrix.
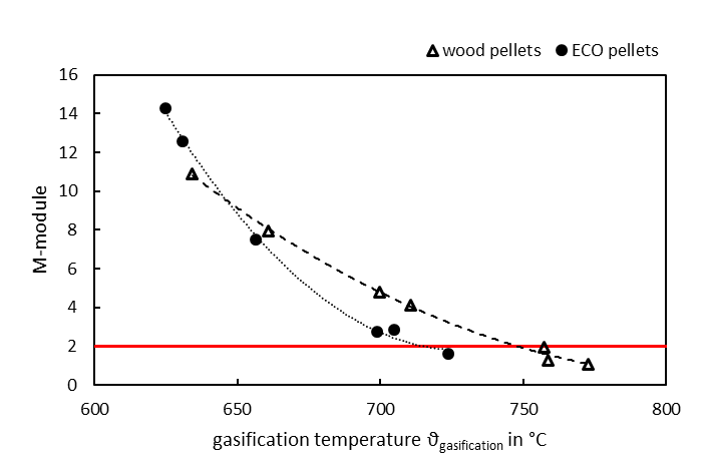
M-module vs. gasification temperature for SEG with wood pellets and ECO pellets.
The gasification temperature has a huge influence on the syngas composition, as it influences the biomass conversion as well as the amount of CO2 that can be captured by the bed material. Therefore the syngas composition can be adjusted flexibly by variation of the gasification temperature, which can be seen in the diagram on the left. For the synthesis of Dimethyl Ether, a syngas composition resulting in a module M of 2 is required. According to the experiments that were conducted, this composition can be achieved at about 715 °C for SEG with ECO pellets and at about 745 °C for SEG with wood pellets.
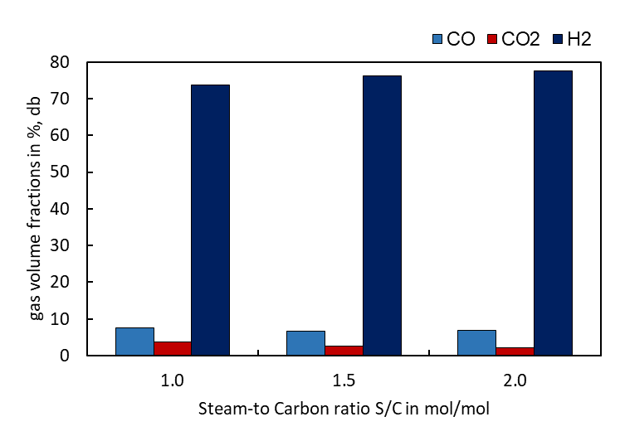
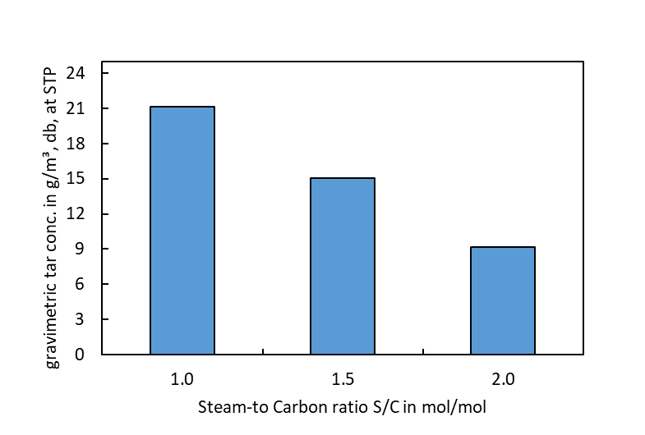
Experiments at the ICB-CSIC 30 kWth bubbling fluidized bed gasifier using wood pellets
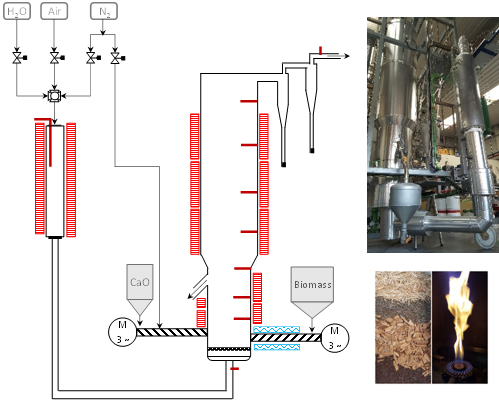
Configuration of the 30 kWth bubbling fluidised bed reactor at ICB-CSIC.
In the 30 kWth BFB facility at ICB-CSIC, the evaluation of the Sorption Enhanced Gasification (SEG) performance has been undertaken using 6 different biomasses as feedstocks. Concretely, it has been studied the influence that the gasification temperature, the steam-to-biomass ratio and the sorbent-to-biomass ratio had on the syngas yield and syngas composition as well as in solids conversion and tar production and composition.
The overall objective of the experiments performed has been evaluating the influence of each operating variable mentioned independently, as well as analyzing the effect of the biomass used in the SEG performance.
Gasification temperature had a great impact on the gas yield through char conversion, making the gas yield to increase as the gasification temperature increases. Gasification temperature was also the main variable affecting syngas composition, even if the individual effect on each gas compound was not the same. Light hydrocarbons (CH4, C2H6, C2H4, C2+) and tars increased noticeably when reducing the gasifier temperature, making the conditioning steps needed before the subsequent synthesis process. However, H2, CO and CO2 behave in the opposite way, increasing their production when gasification temperature was raised.
Differences in the total gas yield were also found depending on the type of biomass used due to the different volatile content.
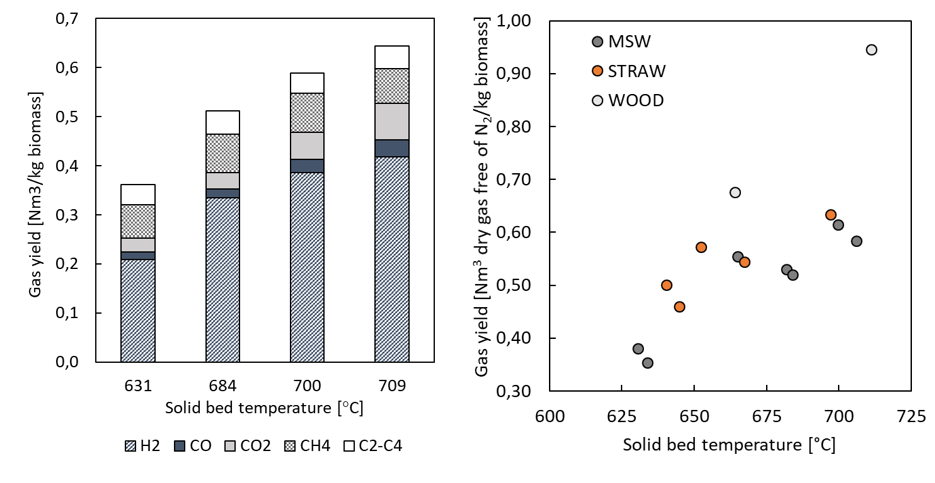
All the results obtained at the ICB-CSIC facility have been included in the public deliverable 2.5 available in the dedicated section of the website, as well as in the scientific papers published.
3D modelling of large scale SEG process (LUT)
LUT has continued activities with Sorption-Enhanced Gasification (SEG) modelling. Recently a new 3D model for connected SEG reactor system has been calibrated on data from University of Stuttgart and CSIC experiments. Model supported design work has been carried out for large scale SEG process in scale of 100MWth. As a result of the design work, reactors with height of 20m and inner diameter approximately 3m were found to be suitable for large scale SEG process.
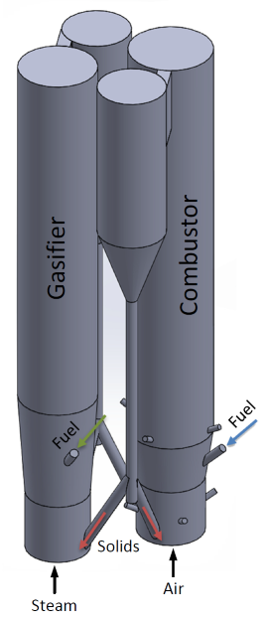
Detailed 3D simulations have been conducted to investigate SEG operation at two operation points. These operation points represents reference (OP1) and flexible operation (OP10), without and with hydrogen enhanced producer gas, respectively. In both operation points, gasifier producer gas ending up to DME synthesis after downstream process components has a composition expressed as Module equal to 2. Different operation points for the SEG process have been achieved by adjusting the gasifier temperature. The main control parameters for gasifier temperature are fuel ratio to reactors and solid circulation rate between the reactors. The following 3D simulation results for the SEG process illustrates estimated local conditions inside the reactors.
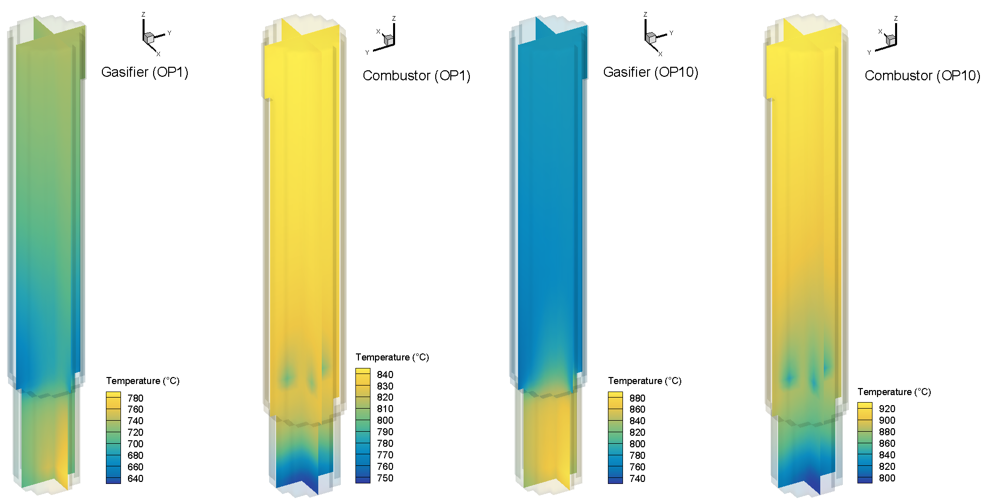
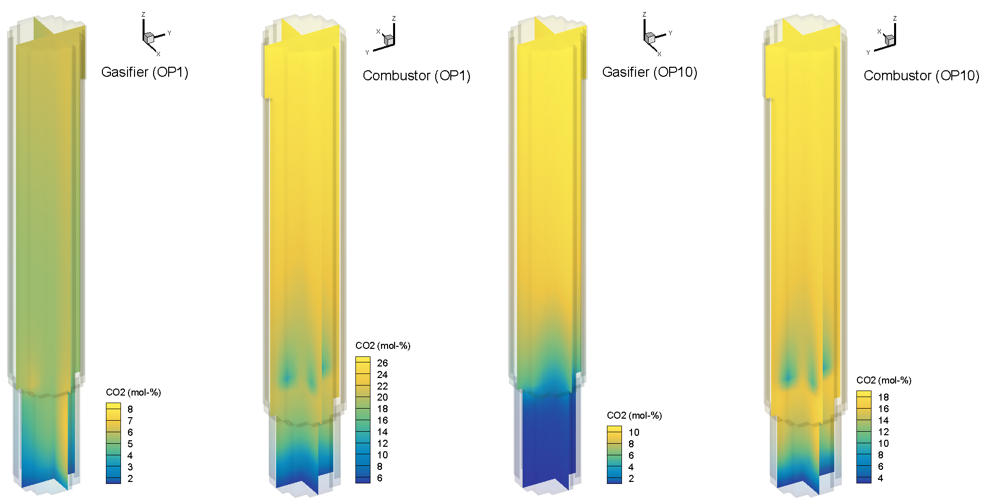
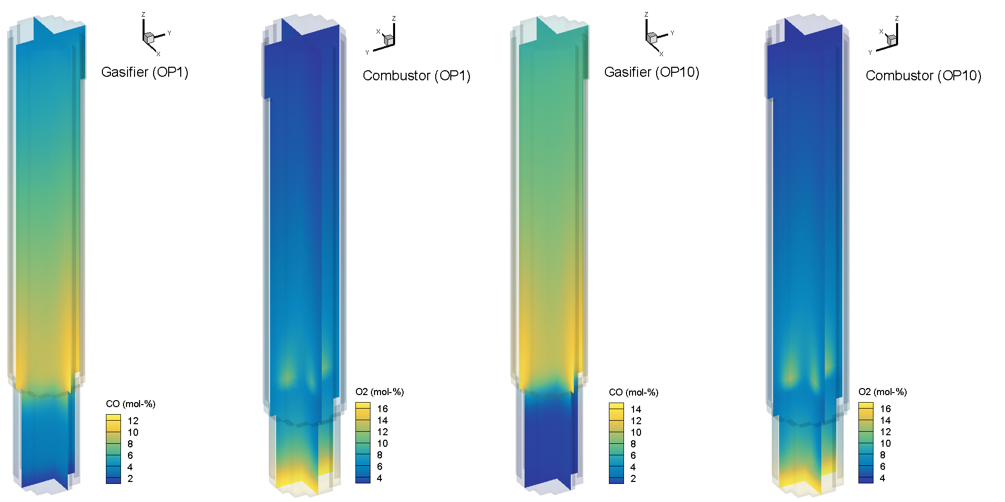
Scientific publications
Simulation of a sorbent enhanced gasification pilot reactor and validation of reactor model (Antti Pitkäojaa, Jouni Ritvanen, Selina Hafner, Timo Hyppänen, Günter Scheffknecht, Energy Conversion and Management, Volume 204, 2020)
Abstract
Sorption enhanced gasification (SEG) is a promising technology for production of a renewable feedstock gas for biofuel synthesis processes. The technology has been previously demonstrated at pilot scale. Scaling of the technology to an industrial size requires knowledge from governing phenomena. One-dimensional bubbling fluidized bed (BFB) reactor model was developed and validated against experimental data from 200kWth dual fluidized bed facility. Sub-models for biomass gasification, reactive bed material and fluidized bed hydrodynamics were incorporated into the model frame. The model gave satisfactory predictions for bed material conversion, temperature profiles and gas composition of the producer gas. The conducted validation improved understanding of bed material conversion, water–gas shift reaction and hydrodynamics and their role in SEG reactors. Further refinement and comprehensive validation of the model with additional data from the pilot is required. The knowledge from the comprehensive validation can be utilized in simulation of an industrial size reactor.